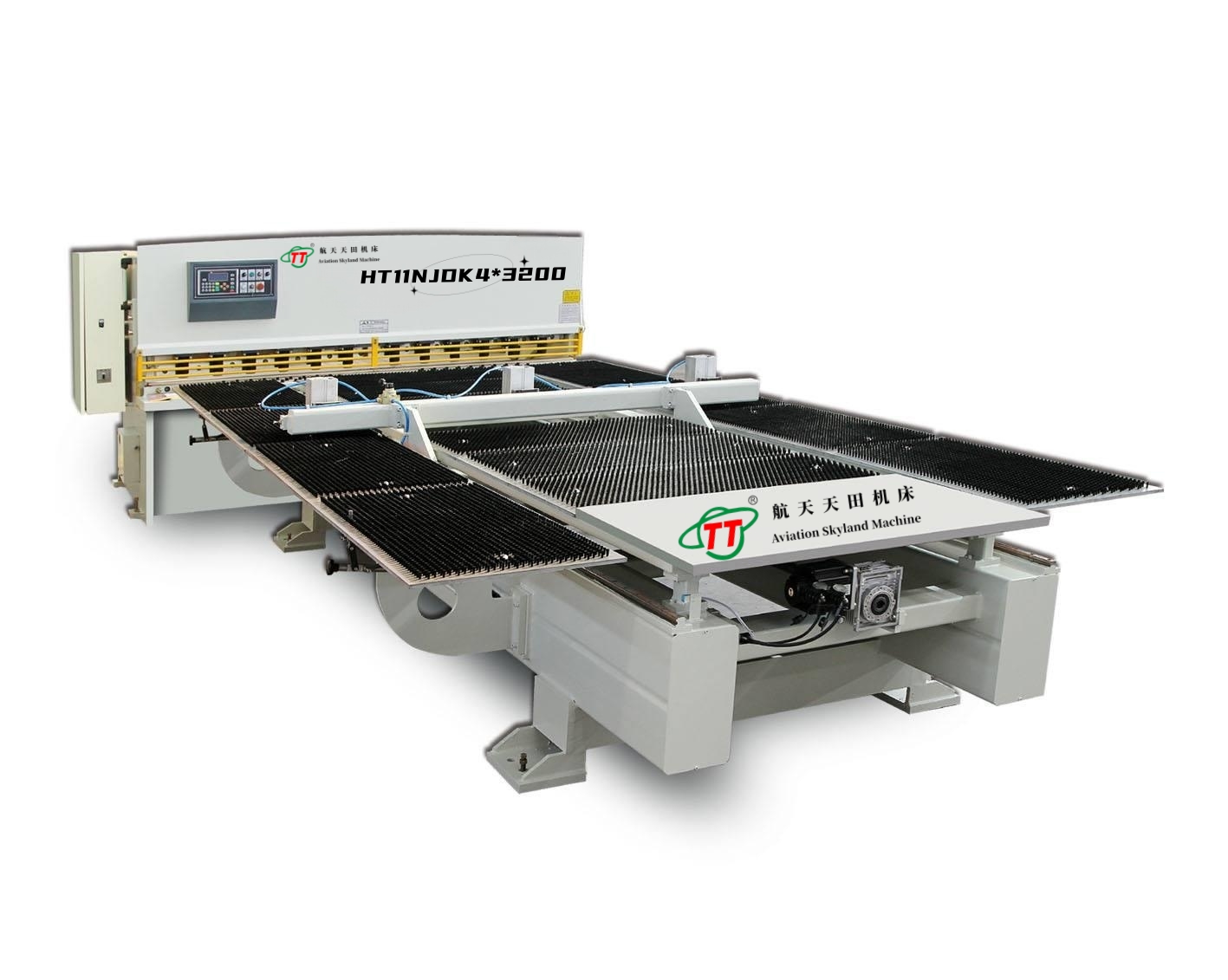
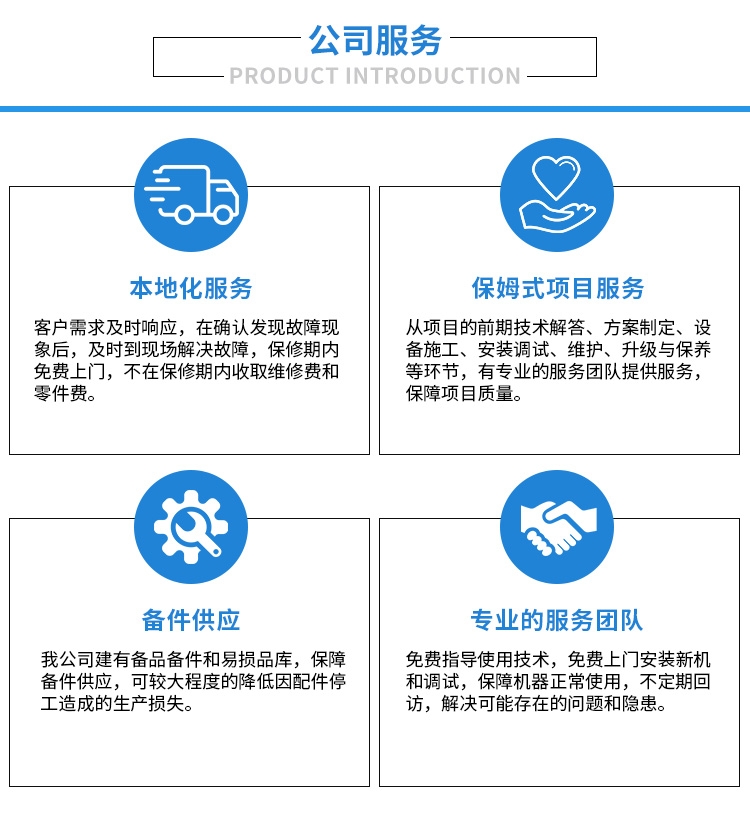
数控前送料剪板机工作原理(Working Principle of the CNC Front-feeding Plate Shearing Machine):
数控前送料剪板机是一种自动化程度较高的金属板材加工设备,它结合了数控技术和前送料系统,能够精确地对板材进行剪切操作。以下是其工作原理的详细介绍:
上料:工人将待加工的金属板材放置在剪板机的前送料装置上,如送料平台或送料辊道。也可通过自动化上料设备,如机械手或吸盘装置,将板材准确地放置到送料位置。
送料控制:数控系统根据预先输入的加工参数,如板材长度、剪切次数等,控制送料装置的运动。送料装置通常由伺服电机驱动,通过滚珠丝杠或同步带等传动机构,带动板材向前移动。伺服电机能够精确控制送料的速度和位置,确保板材每次输送的精度。
定位:当板材输送到指定位置时,送料装置会停止运动,同时定位装置会对板材进行精确的定位,以保证剪切位置的准确性。定位装置可以是机械挡块、光电传感器或激光定位系统等。
刀具驱动:剪板机的剪切刀具由液压系统或机械传动系统驱动。在液压驱动的剪板机中,液压泵将高压油输送到液压缸,推动刀具上下运动;在机械传动的剪板机中,电机通过皮带、齿轮等传动机构带动刀具运动。
剪切力计算:数控系统会根据板材的材质、厚度和宽度等参数,计算出所需的剪切力,并控制液压系统或机械传动系统提供相应的动力,确保刀具能够顺利地切断板材。
刀具闭合:当板材定位完成后,数控系统发出指令,驱动刀具向下运动,与下刀片闭合,对板材进行剪切。刀具的运动速度和行程也由数控系统精确控制,以保证剪切质量。
参数设置:操作人员通过数控系统的操作界面,输入板材的尺寸、材质、剪切长度、剪切次数等加工参数。数控系统会根据这些参数自动生成加工方案,并控制送料装置和剪切刀具的运动。
实时监控:在加工过程中,数控系统会实时监控送料装置和剪切刀具的运动状态,如位置、速度、压力等。如果发现异常情况,如送料偏差、刀具磨损等,数控系统会及时发出警报,并自动调整加工参数或停止加工,以保证加工质量和设备安全。
数据存储和调用:数控系统可以存储多个加工方案,操作人员可以根据需要随时调用这些方案,提高加工效率。同时,数控系统还可以记录加工过程中的各种数据,如加工时间、剪切次数、板材消耗等,方便进行生产管理和质量追溯。
The CNC front-feeding plate shearing machine is a metal plate processing equipment with a high degree of automation. It combines CNC technology with a front-feeding system and can accurately perform shearing operations on metal plates. The following is a detailed introduction to its working principle:
Loading: Workers place the metal plates to be processed on the front-feeding device of the plate shearing machine, such as the feeding platform or the feeding roller table. Automated loading equipment, such as manipulators or suction cup devices, can also be used to accurately place the plates in the feeding position.
Feeding Control: According to the pre-input processing parameters, such as the plate length and the number of shearing times, the CNC system controls the movement of the feeding device. The feeding device is usually driven by a servo motor, and the plate is driven to move forward through transmission mechanisms such as ball screws or synchronous belts. The servo motor can precisely control the feeding speed and position to ensure the accuracy of each plate feeding.
Positioning: When the plate is conveyed to the specified position, the feeding device will stop moving. At the same time, the positioning device will accurately position the plate to ensure the accuracy of the shearing position. The positioning device can be a mechanical stop, a photoelectric sensor, or a laser positioning system, etc.
Tool Drive: The shearing tool of the plate shearing machine is driven by a hydraulic system or a mechanical transmission system. In a hydraulically driven plate shearing machine, the hydraulic pump delivers high-pressure oil to the hydraulic cylinder to push the tool to move up and down. In a mechanically driven plate shearing machine, the motor drives the tool to move through transmission mechanisms such as belts and gears.
Shearing Force Calculation: The CNC system will calculate the required shearing force according to parameters such as the material, thickness, and width of the plate, and control the hydraulic system or the mechanical transmission system to provide the corresponding power to ensure that the tool can smoothly cut off the plate.
Tool Closing: After the plate is positioned, the CNC system issues an instruction to drive the tool to move downward and close with the lower blade to shear the plate. The movement speed and stroke of the tool are also precisely controlled by the CNC system to ensure the shearing quality.
Parameter Setting: The operator inputs processing parameters such as the size, material, shearing length, and the number of shearing times of the plate through the operation interface of the CNC system. The CNC system will automatically generate a processing plan according to these parameters and control the movement of the feeding device and the shearing tool.
Real-time Monitoring: During the processing, the CNC system will monitor the movement status of the feeding device and the shearing tool in real time, such as position, speed, and pressure. If an abnormal situation is detected, such as feeding deviation or tool wear, the CNC system will promptly issue an alarm and automatically adjust the processing parameters or stop the processing to ensure the processing quality and equipment safety.
Data Storage and Retrieval: The CNC system can store multiple processing plans, and the operator can call these plans at any time as needed to improve processing efficiency. At the same time, the CNC system can also record various data during the processing, such as processing time, the number of shearing times, and plate consumption, which is convenient for production management and quality traceability.
Scrap Separation: After the shearing is completed, the plate is cut into the required length, and the scrap will be discharged from the scrap outlet of the plate shearing machine. Some plate shearing machines are also equipped with a scrap separation device, which can automatically separate the scrap from the finished plate to improve production efficiency.
Scrap Collection: The discharged scrap will be collected in a scrap bin or a scrap conveyor for subsequent processing, such as recycling or disposal as waste.
数控前送料剪板机的操作流程是怎样的?
检查设备:查看设备外观有无损坏,各部件是否正常,润滑系统是否工作良好,液压油、润滑油液位是否在正常范围内,电气系统是否正常,各按钮、开关是否灵敏。
准备工具和材料:准备好所需的板材,确保板材表面平整、无杂质,尺寸符合加工要求。同时准备好相应的测量工具,如卡尺、卷尺等,以便对板材进行测量和检验。
安装刀具:根据加工要求选择合适的刀具,安装时要确保刀具安装牢固,刀刃间隙调整合理。一般来说,刀刃间隙要根据板材的材质和厚度进行调整,材质较硬、厚度较大的板材需要较大的刀刃间隙。
开启电源:打开设备电源开关,启动数控系统,等待系统自检完成。
参数设置:根据板材的材质、厚度、长度、宽度等参数,在数控系统中设置相应的剪切参数,如剪切角度、刀片间隙、剪程等。同时,设置前送料的相关参数,如送料速度、送料长度等。
编写程序:如果需要进行批量生产或复杂形状的剪切,可以在数控系统中编写剪切程序。程序可以根据实际需求进行编辑,包括板材的定位、送料、剪切等动作的顺序和参数。
放置板材:将待加工的板材放置在剪板机的前送料操作平台上,注意板材的放置方向和位置要符合加工要求,并且要放置平稳,避免板材在送料过程中发生晃动或偏移。
定位板材:通过数控系统控制前送料装置,将板材准确地定位到剪切位置。在定位过程中,可以使用测量工具对板材的位置进行检查和调整,确保板材的定位精度符合要求。
启动剪切:确认板材定位无误后,按下启动按钮,剪板机开始按照预设的程序和参数进行剪切加工。在剪切过程中,要注意观察设备的运行状态,如刀具的切削情况、板材的送料情况等,如有异常应及时停机处理。
监控加工过程:操作人员应时刻关注剪切过程,确保板材的剪切质量。如果发现剪切尺寸不准确、切口不平整等问题,应及时调整相关参数或停止设备进行检查和维修。
完成剪切:当板材完成剪切后,剪板机自动停止运行。此时,操作人员可以将剪切好的板材取下,并进行下一次的上料和剪切操作。
清理工作区域:加工结束后,关闭设备电源,清理工作区域,将剪下的废料收集起来,保持工作环境的整洁。
保养设备:对剪板机进行日常保养,如清理刀具、润滑各运动部件、清理机床导轨等,以延长设备的使用寿命和保证设备的性能。
记录数据:记录本次加工的相关数据,如板材的材质、规格、加工数量、加工时间等,以便于生产管理和质量追溯。
What is the operating procedure of the CNC front-feeding plate shearing machine?
Preparatory Work
Inspect the Equipment: Check the appearance of the equipment for any damage. Ensure that all components are in normal condition, the lubrication system is functioning properly, the levels of hydraulic oil and lubricating oil are within the normal range, the electrical system is operating normally, and all buttons and switches are sensitive.
Prepare Tools and Materials: Prepare the required plates, ensuring that the surface of the plates is flat, free of impurities, and their dimensions meet the processing requirements. At the same time, prepare corresponding measuring tools such as calipers and tape measures to measure and inspect the plates.
Install the Cutting Tools: Select appropriate cutting tools according to the processing requirements. When installing the tools, make sure they are firmly fixed and the clearance between the cutting edges is adjusted reasonably. Generally speaking, the clearance between the cutting edges should be adjusted according to the material and thickness of the plate. Plates with harder materials and greater thickness require a larger clearance between the cutting edges.
Program Setting
Power On: Turn on the power switch of the equipment and start the CNC system. Wait for the system to complete the self-check.
Parameter Setting: According to parameters such as the material, thickness, length, and width of the plate, set the corresponding shearing parameters in the CNC system, such as the shearing angle, the clearance of the blades, and the shearing stroke. Meanwhile, set the relevant parameters for front feeding, such as the feeding speed and the feeding length.
Program Compilation: If batch production or shearing of complex shapes is required, a shearing program can be compiled in the CNC system. The program can be edited according to actual needs, including the sequence and parameters of actions such as the positioning, feeding, and shearing of the plate.
Plate Loading
Place the Plate: Place the plate to be processed on the front-feeding operation platform of the plate shearing machine. Pay attention that the placement direction and position of the plate should meet the processing requirements, and the plate should be placed steadily to avoid shaking or deviation during the feeding process.
Position the Plate: Control the front-feeding device through the CNC system to accurately position the plate at the shearing position. During the positioning process, measuring tools can be used to check and adjust the position of the plate to ensure that the positioning accuracy of the plate meets the requirements.
Shearing Process
Start Shearing: After confirming that the plate is positioned correctly, press the start button, and the plate shearing machine will start the shearing process according to the preset program and parameters. During the shearing process, pay attention to observing the operation status of the equipment, such as the cutting condition of the tools and the feeding condition of the plate. If any abnormalities occur, stop the machine immediately for handling.
Monitor the Processing: The operator should always pay attention to the shearing process to ensure the shearing quality of the plate. If problems such as inaccurate shearing dimensions or uneven cutting edges are found, adjust the relevant parameters in a timely manner or stop the equipment for inspection and maintenance.
Complete Shearing: When the plate is sheared, the plate shearing machine will stop running automatically. At this time, the operator can remove the sheared plate and proceed with the next loading and shearing operation.
After Processing
Clean the Working Area: After the processing is completed, turn off the power of the equipment, clean the working area, collect the cut waste materials, and keep the working environment clean.
Maintain the Equipment: Conduct daily maintenance on the plate shearing machine, such as cleaning the cutting tools, lubricating all moving parts, and cleaning the machine tool guide rails, to extend the service life of the equipment and ensure its performance.
Record Data: Record the relevant data of this processing, such as the material and specification of the plate, the processing quantity, and the processing time, to facilitate production management and quality traceability.
一、性能特点//
1:主机采用HT11K系列数控闸式剪板机;
2:采用荷兰进口DELEM公司DAC360数控系统,双轴数控。
3:配备前送料操作平台 。
二、荷兰DELEM公司 DAC360 数控系统简介:
1、该数控系统为数控液压闸式剪板机通用控制系统。
2、高清晰的LCD显示240*64点阵。
3、国际通用的RS232标准接口方便与计算机连接。
4、1000个程序行,每个程序最大25步,每步可重复99次。
5、控制三个伺服轴,X1-X2可同步进给。
6、可自动控制剪切角、刀片间隙、剪程等模拟轴。
7、可自动或手动进行参考点搜索,也可在断电后自动记忆最后实际位置的数值。
8、具有补偿功能。若剪出的板材长度与设定的数值有小的误差,因为板料的拱凸等原因从而使得实际剪切长度有误差。
9、具有后挡料退让功能,在厚的板材进行剪板时为了防止板材发生变形挤压刀具和保护丝杆,当压紧油缸压到板材时后挡料可实现退让功能。
三、技术特性 :
1. 机架采用全钢焊接结构,有足够的强度及刚性,并通过正火及高频振动消除内应力,保证机身的整体精度。
2. 采用大型落地镗铣床,用一次加工法,作精密加工,以确保加工精度。
3. 液压闸式结构,三点支承滚动轴承,消除支承间隙,提高剪切精度。
4. 液压系统采用整体式逻辑回路,动作平稳,噪音低,维护简单。
5. 采用日本NOK密封圈;专业制作的油缸控制刀板运行。
6. 压料装置采用整体回路及独立式并列压紧缸。当板料不平时,可自由伸缩压紧在板料上。
7. 通过电气进行控制,可实现定程剪切,且剪切行程可调。
8. 电气控制集中可靠,具体如下:
动力设施均设于机身内,通过控制面板的按钮,进行操作来控制和实现。设有脚踏开关,可通过其直接对剪切动作进行操作,方便快捷。电机的过载和短路,通过空气开关进行保护。
9. 液压系统安全可靠
10. 上下刀采用优质HK13/6Crw2si或进口DA53材料,并全部经热处理, 以确保其具有足够的硬度及较长的使用寿命。
11. 滚球式工作台及前托料装置,送料方便,并保证工件在运行时不被划伤。数控后档料装置采用高性能伺服电机及驱动,精密滚珠丝杆传动定位精度 ≤±0.15mm。
12.采用荷兰DELEM公司的DAC360剪板机专用数控系统,精确控制剪切角度和间隙。
I. Performance Characteristics
The main machine adopts the HT11K series CNC guillotine plate shearing machine.
It adopts the DAC360 CNC system imported from DELEM Company in the Netherlands, which is a dual-axis CNC system.
It is equipped with a front-feeding operation platform.
II. Introduction to the DAC360 CNC System of DELEM Company in the Netherlands:
This CNC system is a general control system for CNC hydraulic guillotine plate shearing machines.
It has a high-definition LCD display with a 240*64 dot matrix.
The internationally universal RS232 standard interface makes it convenient to connect with a computer.
There are 1000 program lines, with a maximum of 25 steps in each program, and each step can be repeated 99 times.
It controls three servo axes, and X1-X2 can feed synchronously.
It can automatically control analog axes such as the shearing angle, blade clearance, and shearing stroke.
It can automatically or manually search for the reference point, and can also automatically memorize the value of the last actual position after a power outage.
It has a compensation function. If there is a small error between the length of the cut plate and the set value, for reasons such as the arching of the plate, the actual shearing length will have an error.
It has a rear stop gauge retraction function. When shearing thick plates, in order to prevent the plate from deforming and squeezing the tool and protect the lead screw, the rear stop gauge can achieve the retraction function when the clamping cylinder presses against the plate.
III. Technical Characteristics:
The frame adopts an all-steel welded structure, which has sufficient strength and rigidity. And through normalizing and high-frequency vibration, the internal stress is eliminated to ensure the overall accuracy of the machine body.
A large-scale floor-type boring and milling machine is used, and the precision machining is carried out by the one-time machining method to ensure the machining accuracy.
The hydraulic guillotine structure with three-point supported rolling bearings eliminates the support clearance and improves the shearing accuracy.
The hydraulic system adopts an integral logic circuit, with stable operation, low noise, and simple maintenance.
Japanese NOK seals are used; specially made oil cylinders control the operation of the knife plate.
The material pressing device adopts an integral circuit and independent parallel clamping cylinders. When the plate is uneven, it can freely stretch and press against the plate.
It is controlled by electricity, and fixed-stroke shearing can be realized, and the shearing stroke is adjustable.
The electrical control is centralized and reliable, as follows:
The power facilities are all installed inside the machine body, and the operation, control, and realization are carried out through the buttons on the control panel. A foot switch is provided, and the shearing action can be directly operated through it, which is convenient and fast. The overload and short circuit of the motor are protected by an air switch.
The hydraulic system is safe and reliable.
The upper and lower knives are made of high-quality HK13/6Crw2si or imported DA53 materials, and all are heat-treated to ensure that they have sufficient hardness and a long service life.
The ball-type worktable and the front material supporting device make the feeding convenient and ensure that the workpiece is not scratched during operation. The CNC rear stop gauge device adopts high-performance servo motors and drivers, and the precision ball screw drive positioning accuracy is ≤±0.15mm.
The DAC360 special CNC system for plate shearing machines of DELEM Company in the Netherlands is adopted to precisely control the shearing angle and clearance.
四、主要进口配置清单:1 | 数控系统 | 1套 | 荷兰DELEM 公司DAC360 |
2 | 伺服电机及驱动 | 1套 | 埃斯顿 |
3 | 液压系统 | 1套 | 德国力士乐 |
4 | 滚珠丝杠 | 2根 | 台湾HIWIN |
5 | 接头 | 1套 | 德国派克 |
6 | 密封圈 | 1套 | 日本VALQUA |
7 | 主要电器元件 | 1套 | 荷兰DELEM 公司 |
8 | 齿轮泵 | 1个 | 上海航发 |
IV. List of Main Imported Configuration Items:
CNC System: 1 set, DAC360 from DELEM Company in the Netherlands
Servo Motor and Driver: 1 set, Estun
Hydraulic System: 1 set, Rexroth from Germany
Ball Screws: 2 pieces, HIWIN from Taiwan
Connectors: 1 set, Parker from Germany
Sealing Rings: 1 set, VALQUA from Japan
Main Electrical Components: 1 set, DELEM Company in the Netherlands
Gear Pump: 1 piece, Shanghai Hangfa
五、HT11K液压板料数控剪板机技术参数表(Technical Parameter Table of CNC Hydraulic Plate Shearing Machine):设备型号
Equipment Model | 可剪板材规格
Specifications of
Shearable Plate
Materials
(长*宽)(mm) | 剪切角(°)
Shearing angle | 行程次数(n/min)
Number of strokes | 后挡料距离(mm)
Distance of the
rear stop gauge | 电机功率(kw)
Motor power | 重量(kg)
weight | 外形尺寸(长*宽*高)
Overall Dimensions
(Length * Width * Height) |
HT11K-6*2500 | 6*2500 | 1.5° | 18 | 20-600 | 7.5 | 4800 | 3040mm*8610mm*1650mm |
HT11K-6*3200 | 6*3200 | 1.5° | ≥14 | 20-600 | 7.5 | 5900 | 3840mm*9310mm*1650mm |
HT11K-8*3200 | 8*3200 | 1.5° | ≥10 | 20-600 | 7.5 | 6700 | 3840mm*9310mm*1650mm |
备注:本资料所列数据为参考数据,如与机床实际数据不符,应以机床实际数据为准,
以上参数如有变动,恕不另行通知,本公司保留对此资料的最终解释权!
Remarks: The data listed in this document are for reference only. In case of any discrepancy between these data and the actual data of the machine tool, the actual data of the machine tool shall prevail.
The above parameters are subject to change without prior notice. Our company reserves the right to the final interpretation of this document!