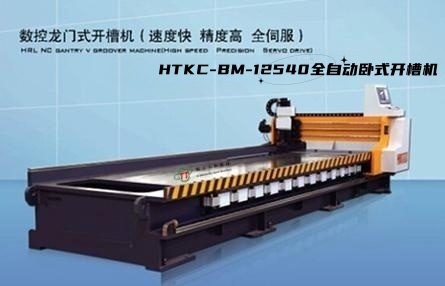
双头或多头卧式数控龙门式开槽机适用于哪些行业?
双头或多头卧式数控龙门式开槽机具有高精度、高效率和高自动化等特点,适用于以下多个行业:
金属加工行业
建筑装饰行业
幕墙加工:在建筑幕墙的制造中,用于对铝合金、钢材等幕墙龙骨材料进行开槽,以便安装玻璃、石材等幕墙面板,保证幕墙的结构强度和稳定性。
门窗加工:对门窗型材进行开槽,用于安装五金配件、密封胶条等,提高门窗的密封性、防水性和美观度。
室内装饰:在室内装饰中,可对各种装饰板材如木板、人造板、石材等进行开槽,用于制作家具、背景墙、装饰线条等,实现不同的造型和装饰效果。
电子电器行业
包装行业
Which industries are double-head or multi-head horizontal CNC gantry grooving machines suitable for?Double-head or multi-head horizontal CNC gantry grooving machines are characterized by high precision, high efficiency, and high automation, and are suitable for the following industries:
Metal Processing Industry
Stainless Steel Processing: It is used for grooving stainless steel sheets to manufacture various stainless steel products, such as stainless steel doors and windows, stainless steel furniture, and stainless steel decorative parts.
Carbon Steel and Alloy Steel Processing: Groove carbon steel, alloy steel, and other metal sheets to meet the processing requirements of components in fields such as machinery manufacturing, automotive manufacturing, and aerospace. For example, the processing of automotive engine blocks, aircraft wing structural components, etc. may use this kind of equipment.
Construction and Decoration Industry
Curtain Wall Processing: In the manufacturing of building curtain walls, it is used to groove curtain wall keel materials such as aluminum alloys and steel to install glass, stone, and other curtain wall panels, ensuring the structural strength and stability of the curtain wall.
Door and Window Processing: Groove door and window profiles to install hardware accessories, sealing rubber strips, etc., improving the airtightness, waterproofness, and aesthetics of doors and windows.
Interior Decoration: In interior decoration, it can groove various decorative sheets such as wood boards, artificial boards, and stones to make furniture, feature walls, decorative moldings, etc., achieving different shapes and decorative effects.
Electronics and Electrical Appliance Industry
Electrical Appliance Shell Processing: Groove the shell materials of electronic and electrical products, such as steel plates and aluminum plates, to install various components, heat sinks, connecting wires, etc., while ensuring the overall strength and aesthetics of the shell. For example, the processing of computer cases, distribution cabinets, and other shells.
Circuit Board Manufacturing: In the production process of circuit boards, a grooving machine may be required to groove the insulating substrate for installing electronic components or for circuit layout.
Packaging Industry
Carton Processing: It is used to groove cardboard for folding into cartons. Through precise grooving, the corners of the cartons can be neat and the dimensions accurate, improving the quality and production efficiency of the cartons.
Wooden Box Processing: Groove wooden boards for making the mortise and tenon structure of wooden boxes or installing accessories such as hinges and handles, enhancing the firmness and practicality of the wooden boxes.
双头或多头卧式数控龙门式开槽机的工作效率有多高?
双头或多头卧式数控龙门式开槽机的工作效率受多种因素影响,包括机床的性能参数、加工材料的特性、开槽的工艺要求等,以下是一些具体分析:
刀具数量和布局:双头或多头设计使得机床能够同时进行多个开槽操作,相比单头开槽机,在单位时间内能够完成更多的开槽任务。例如,一台双头开槽机理论上的开槽效率是单头开槽机的两倍。如果是多头设计,效率提升会更显著,如四头开槽机同时工作,能极大提高加工效率。
切削速度:这类开槽机通常采用高性能的伺服电机驱动,配合先进的数控系统,能够实现较高的切削速度。一般情况下,对于普通金属材料,切削速度可以达到每分钟数十米甚至更高。以加工铝合金板材为例,切削速度可能在 50 - 100 米 / 分钟左右,而对于硬度较高的不锈钢材料,切削速度可能会降低到 30 - 50 米 / 分钟。
进给速度:机床的进给速度也相当可观,一般能达到每分钟数米甚至十几米。例如,在对厚度为 5 毫米的钢板进行开槽加工时,进给速度可能设定在 3 - 8 米 / 分钟。同时,由于采用了高精度的齿轮齿条传动或滚珠丝杠传动,机床在高速进给的情况下仍能保持较高的定位精度,确保开槽的尺寸精度和表面质量。
自动化程度:配备自动上料装置、刀具自动更换系统和自动化喷雾冷却系统等自动化功能,减少了人工上下料和刀具更换的时间,提高了生产效率。自动上料装置可以在短时间内完成板材的上料和定位,通常每小时能够上料数十次甚至更多,具体次数取决于板材的尺寸和重量。刀具自动更换系统能够在数秒内完成刀具的更换,大大缩短了因刀具磨损或损坏而导致的停机时间。
综上所述,双头或多头卧式数控龙门式开槽机的工作效率较高,能够在短时间内完成大量的开槽加工任务。在实际生产中,其具体的工作效率需要根据具体的加工任务和工艺要求来确定。
How high is the working efficiency of the double-head or multi-head horizontal CNC gantry grooving machine?
The working efficiency of the double-head or multi-head horizontal CNC gantry grooving machine is affected by various factors, including the performance parameters of the machine tool, the characteristics of the processed material, and the technological requirements of grooving. Here is a detailed analysis:
Number and Layout of Cutting Tools: The double-head or multi-head design enables the machine tool to perform multiple grooving operations simultaneously. Compared with a single-head grooving machine, it can complete more grooving tasks within a unit of time. For example, theoretically, the grooving efficiency of a double-head grooving machine is twice that of a single-head grooving machine. If it has a multi-head design, the efficiency improvement will be even more significant. For instance, when the four cutting heads of a four-head grooving machine work simultaneously, the processing efficiency can be greatly enhanced.
Cutting Speed: This type of grooving machine usually adopts high-performance servo motors for driving and is equipped with an advanced numerical control system, which can achieve a relatively high cutting speed. Generally speaking, for common metal materials, the cutting speed can reach dozens of meters per minute or even higher. For example, when processing aluminum alloy sheets, the cutting speed may be around 50 - 100 meters per minute, while for stainless steel materials with higher hardness, the cutting speed may decrease to 30 - 50 meters per minute.
Feed Rate: The feed rate of the machine tool is also quite considerable, generally able to reach several meters or even more than ten meters per minute. For example, when grooving a steel plate with a thickness of 5 millimeters, the feed rate may be set at 3 - 8 meters per minute. At the same time, due to the adoption of high-precision gear-rack transmission or ball screw transmission, the machine tool can still maintain a high positioning accuracy during high-speed feeding, ensuring the dimensional accuracy and surface quality of the grooving.
Degree of Automation: It is equipped with automated functions such as an automatic feeding device, an automatic tool changing system, and an automated spray cooling system, which reduces the time for manual loading and unloading of materials and tool changing, thus improving production efficiency. The automatic feeding device can complete the loading and positioning of the sheet material in a short time, usually being able to load materials dozens of times or even more per hour. The specific number of times depends on the size and weight of the sheet material. The automatic tool changing system can complete the tool change within a few seconds, greatly shortening the downtime caused by tool wear or damage.
In conclusion, the double-head or multi-head horizontal CNC gantry grooving machine has a relatively high working efficiency and can complete a large number of grooving processing tasks in a short period. In actual production, its specific working efficiency needs to be determined according to the specific processing tasks and technological requirements.
一、性能特点//
1、HTKC-BM开槽机机座、横梁均采用框架结构设计,工作台面使用50mm低合金高强度结构钢,框架采用高强度Q345钢板,机座整体刚性好,坚固耐用。
2、严格按照机床加工工艺制作,采用整体回火处理,消除焊接应力减少设备变形。
3、通过喷砂处理保证漆面涂装效果清晰美观。
4、HTKC-BM系列开槽机加工件采用气动夹紧系统固定,开槽速度快并保证强力夹紧。
The machine base and crossbeam of the HTKC-BM slotting machine adopt a frame structure design. The worktable surface is made of 50mm low-alloy high-strength structural steel, and the frame is made of high-strength Q345 steel plates. The overall rigidity of the machine base is excellent, and it is sturdy and durable.
It is manufactured in strict accordance with the machining process of machine tools, and undergoes integral tempering treatment to eliminate welding stress and reduce equipment deformation.
The sandblasting treatment ensures that the paint coating effect is clear and aesthetically pleasing.
The workpieces processed by the HTKC-BM series slotting machine are fixed by a pneumatic clamping system, which enables fast slotting speed and ensures powerful clamping force.
二、HTKC-BM系列数控双头或多头刨开槽机参数(Parameters of CNC Double-head or Multi-head Planer Slotting Machine):
序号 Serial numbe | 内容matter | 技术参数 Technical parameters | 技术参数 Technical parameters | 技术参数 Technical parameters | 技术参数 Technical parameters | 技术参数 Technical parameters |
1 | 型号Model | HTKC-BM-12540 | HTKC-BM-12560 | HTKC-BM-1640 | HTKC-BM-1660 | HTKC-BM-1680 |
2 | 加工板厚 The thickness of the plate that can be processed | 0.4-6mm | 0.4-6mm | 0.4-6mm | 0.4-6mm | 0.4-6mm |
3 | 加工板长宽 The length and width of the plate that can be processed | 4000x1250mm | 6000x1250mm | 4000x1600mm | 6000x1600mm | 8000x1600mm |
4 | 切销速度/可否变速(Cutting speed / Can it be variable speed) | 5M-70M/min | 3M-50M/min | 3M-40M/min | 3M-35M/min | 3M-30M/min |
5 | 工作台面调 整 (Adjustment of the worktable surface) | 自刨功能 | 自刨功能 | 自刨功能 | 自刨功能 | 自刨功能 |
6 | X轴最小设定单位(The minimum setting unit of the X-axis) | 0.01mm | 0.01mm | 0.01mm | 0.01mm | 0.01mm |
7 | X轴定位精度(X - axis positioning accuracy) | ±0.05mm | ±0.05mm | ±0.05mm | ±0.05mm | ±0.05mm |
8 | Y轴最小设定单位(The minimum setting unit of the Y-axis) | 0.01mm | 0.01mm | 0.01mm | 0.01mm | 0.01mm |
9 | Y轴定位精度(Y - axis positioning accuracy) | ±0.03mm | ±0.05mm | ±0.05mm | ±0.05mm | ±0.05mm |
10 | Z轴最小设定单位(The minimum setting unit of the Z-axis) | 0.01mm | 0.01mm | 0.01mm | 0.01mm | 0.01mm |
11 | Z轴定位精度(Z - axis positioning accuracy) | ±0.03mm | ±0.03mm | ±0.03mm | ±0.03mm | ±0.03mm |
12 | X1-X2轴电机功率 The motor power of the X1-X2 axis | 1KW-1KW | 1KW-1KW | 1KW-1KW | 1KW-1KW | 1KW-1KW |
13 | Y轴电机功率 (The motor power of the Y-axis) | 4.5KW | 4.5KW | 5.5KW | 7.5KW | 11KW |
14 | Z轴电机功率 The motor power of the Z-axis | 1KW | 1KW | 1.5KW | 1.5KW | 3KW |
15 | 工作台平面度 (Flatness of the worktable surface) | ±0.03mm | ±0.03mm | ±0.03mm | ±0.03mm | ±0.03mm |
16 | 送料方式 Feeding method | 板料不动,刀架移动 The sheet metal remains stationary while the tool holder moves | 板料不动,刀架移动 The sheet metal remains stationary while the tool holder moves | 板料不动,刀架移动 The sheet metal remains stationary while the tool holder moves | 板料不动,刀架移动 The sheet metal remains stationary while the tool holder moves | 板料不动,刀架移动 The sheet metal remains stationary while the tool holder moves |
17 | 工作台可否方便更换 Can the worktable be replaced conveniently | 不可以更换 It cannot be replaced | 不可以更换 It cannot be replaced | 不可以更换 It cannot be replaced | 不可以更换 It cannot be replaced | 不可以更换 It cannot be replaced |
18 | 工作台是否淬火 (Has the worktable been quenched) | 是 Yes | 是 Yes | 是 Yes | 是 Yes | 是 Yes |
19 | 安装刀数(The quantity of installed knives) | 4把 | 4把 | 4把 | 4把 | 4把 |
20 | 最大一次刨深 (Maximum single-pass planing depth) | 0.8mm | 0.8mm | 1.0mm | 1.2mm | 1.5mm |
21 | 最大开槽深度(Maximum slotting depth) | 2.5mm | 2.5mm | 3mm | 4mm | 6mm |
31 | 冷却喷雾器 (Cooling sprayer) | 有 | 有 | 有 | 有 | 有 |
33 | 售后服务 (After-sales service) | 1年保修 It comes with a one-year free warranty | 1年保修 It comes with a one-year free warranty | 1年保修 It comes with a one-year free warranty | 1年保修 It comes with a one-year free warranty | 1年保修 It comes with a one-year free warranty |
三、机床主要性能特点:1、龙门式,上下料方便。
2、液压控制系统,加工过程中,不会松板,不会压花板,压力稳定可靠。
四、机床的性能和主要特点:
1、机身全钢焊接,经退火热处理,削除内应力,具有极高的的强度,机身不变形。
2、采用台湾伊斯凯特数控系统,技术成熟,产品性能可靠。
3、电器全部采用法国施耐德公司的产品,保证了电路的使用寿命及稳定性。
4、台湾油研的液压控制系统,压板、钳口的压紧及松开全自动化,压力稳定可靠。
5、伺服馬达进刀,精度高且可靠,可达0.01mm。
6、伺服馬达控制刀架及送料装置,刨削及定位精准。
7、采用触摸屏,指令输入快捷明晰。
8、改传统螺母丝杆传动方式为进口精麿合金钢齿轮齿条传动,更易维护,故障率更低。
9、回程速度快,效率高,运行更平稳.静音。
10、自动化喷雾方式对刀具进行冷却,提高刀具使用寿命。
III. Main Performance Characteristics of the Machine Tool:
It has a gantry structure, which makes loading and unloading convenient.
With a hydraulic control system, during the processing, the plate will not loosen and there will be no embossing on the plate. The pressure is stable and reliable.
IV. Performance and Main Features of the Machine Tool:
The machine body is fully welded with steel and has undergone annealing heat treatment to eliminate internal stress. It has extremely high strength and the machine body will not deform.
It adopts the numerical control system of Taiwan Is 凯特 (It's recommended to confirm the accurate English name of "伊斯凯特", here "Is 凯特" is just a literal translation). The technology is mature and the product performance is reliable.
All electrical appliances are products of Schneider Electric Company in France, which ensures the service life and stability of the circuit.
With the hydraulic control system of YUKEN in Taiwan, the pressing and releasing of the pressing plate and the clamping jaw are fully automated, and the pressure is stable and reliable.
The servo motor is used for feeding, which is highly accurate and reliable, and the accuracy can reach 0.01mm.
The servo motor controls the tool holder and the feeding device, ensuring precise planing and positioning.
It is equipped with a touch screen, enabling quick and clear command input.
It changes the traditional transmission mode of nut and screw rod to the transmission of imported precision-ground alloy steel gear and rack, which is easier to maintain and has a lower failure rate.
It has a fast return stroke speed, high efficiency, smoother operation and is silent.
The tool is cooled by an automated spraying method, which improves the service life of the tool。
本资料所列数据为参考数据,如与机床实际数据不符,应以机床实际数据为准,
以上参数如有变动,恕不另行通知,本公司保留对此资料的最终解释权!
The data listed in this document are for reference only. In case of any discrepancy between these data and the actual data of the machine tool, the actual data of the machine tool shall prevail.
The above parameters are subject to change without prior notice. Our company reserves the right to the final interpretation of this document!